Fenike's new product launch conference introduces several new CBN tools
2023-04-05 09:06:39
On October 26th, Fu Nike CBN tool new product release and technical exchange meeting was held in Zhengzhou Jiangnan Spring Hot Spring Hotel. At the press conference, Mr. Zhang Taihe, Chief Engineer of Henan Fenike Superhard Materials Co., Ltd., gave a key introduction to several new CBN tools to more than 100 CBN tool application representatives and industry media.
Mr. Zhang Taihe, Chief Engineer of Henan Fenike Superhard Materials Co., Ltd., promotes new CBN tool products . 1. Fu Nike CBN super welding tool
Super-welded FBS blade compared to composite CBN blade
Common problems of common composite CBN insert CBN inserts on the market are: 1. CBN layer and cemented carbide substrate open layer; 2. CBN cutting edge desoldering; 3. Cutting edge easy to chip, resistance to cutting impact; 4. Application range narrow.
Features of Fenike's super-welded CBN inserts: 1. The overall CBN polycrystalline crystal is directly welded to the blade base to form a growth-type super-strong structure with no chance of opening and cracking. 2. Thicker CBN polycrystalline crystals have higher impact resistance than the existing silver bonded CBN composite inserts.
3. It adopts special welding technology, flux and welding method independently developed and has high temperature resistance above 1000 °C. 4. The universal clamping method can be directly clamped on the existing cutter body. 5. Multi-standard, multi-variety, can adapt to the needs of more occasions processing. 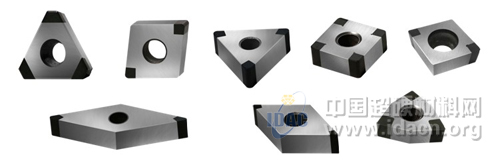
CBN blade performance comparison
October 2009 - Super Welding Patent
Case 1. FBS super welding blade roughing
Case 2. FBS super welding blade finishing
Application of Intermittent Rough Machining of Super-strong Welding CBN Tools
Application of super-strong welding CBN tool intermittent finishing: Workpiece: Automotive transmission inner wheel (spherical drive shaft) Workpiece material: Hardened steel HRC58~62 Machine tool: Double-axis vertical car processing: In-vehicle spherical roughness Ra1.2 Dimensional accuracy +0.03mm Tool: TNGA160416 S02020 FBS7000 Cutting parameters: Vc=180m/min f=0.17mm/r Ap=0.3 Dry cutting tool life: 200-400 pieces/blade 2. Fu Nike new grade FBN6000 Features: (1) Suitable for ash Roughing and semi-finishing of materials such as iron, ductile iron, and high hardness alloy cast iron. (2) Suitable for roughing and semi-finishing of hardness greater than HRC45 alloy steel, hardened steel. (3) Suitable for high speed continuous cutting and medium and low speed interrupted cutting. Fu Nike's new grade FBN6000: Compared with FBN3500, it maintains FBN3500's impact resistance and can improve wear resistance by more than 30%, which can meet the rough and semi-finishing of high hardness cast iron and high hardness steel. FBN6000: It is an integrated polycrystalline CBN blade and is an upgraded product of FBN3500.
Case 1. FBN6000 rough car high nickel chrome cast iron roll
Performance comparison (alloy cast iron rolls)
Case 2. FBN6000 rough car high carbon semi-steel roll
Case 3. Application of FBN6000 processing gearbox 3. Fenike new grade FBS7000 Features: (1) High wear resistance and high impact resistance; (2) Can process both cast iron and hardened steel; (3) Dry cutting Wet cutting; (4) Continuous and intermittent turning and milling. 
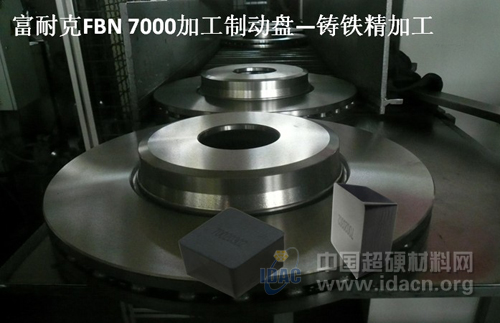
Performance comparison (brake disc)
Fu Nike FBS 7000 interrupted machining gear - hardened steel finishing
Performance comparison (carburized steel gear)
FBN7000 intermittent wet cutting
FBS7000 intermittent dry cutting
FBn7000 processing wind power bearing
FBN7000 processing wear plate III. CBN tool failure analysis In the production practice of machining, the main performance of tool failure is: blade wear, chipping, fracture. (1) wear; ◠flank wear: generally occurs in brittle materials. The main feature of CBN series tool wear is slow wear, but if it is used improperly, it can be sharply worn. The sharp wear occurs when the cutting temperature is too high, the cutting speed is high, and the cutting temperature is high. The main way to solve the sharp wear is to adjust the cutting speed. Practices from cutting have shown that PCBN inserts also undergo "reversible conversion" when the cutting zone temperature exceeds 1200°.
â—The front and rear flank wear at the same time: the front and back flank wear at the same time (such as "severe crater"), indicating that the cutting area has exceeded 1200 °C, phase change wear occurs, even the high inert CBN tool is no exception, it may happen Different degrees of diffusion, the solution is mainly to adjust the cutting speed and feed. (2) The chipping blade cannot withstand the existing cutting force, cutting vibration, cutting impact and other processing conditions, and generally can hear abnormal cutting sound and vibration. The problem of solving the chipping is mainly to improve the cutting force and cutting vibration of the blade. The solutions are as follows:
A tool angle improvement B edge form improvement C cutting parameter improvement (3) fracture
The main reasons for the breakage of the blade are: â— The reason of the cutter itself; the bottom of the blade is not flat, the blade is not flat, and the cutting edge is seriously worn. â—Cause of the cutting process: Since the working layer of the high-speed steel roll contains a large amount of high-hardness carbide, the cutting process has a scratching effect on the cutting edge, and the groove wear of the cutting edge occurs. In the continuous impact of the chips for a long time, the final blade is difficult to bear, leading to breakage. â—Usage problem: the tool hits the knife during the cutting process, crashes, the blade has a gap, the severe wear does not change the blade, and the feed rate is too large. Revelation often has a habitual practice. If there is a problem with the cutting process, it is considered that the tool is out of order, and a lot of work and solutions are carried out around the tool. In fact, cutting is a system problem. The tool is a part of this system. In the cutting process, the machine tool, workpiece blank, fixture, clamping method, cutting fluid, etc. constitute a system. The tool is a subsystem in this part, including tool structure, compression method, toolholder manufacturing accuracy, tool pad material, tool angle, blade size, thickness and cutting parameters. All the factors are combined to affect the accuracy and efficiency of the product. Any change in the overall system will have an impact on the system's output - and processing efficiency and processing results. Therefore, to maximize the role of the tool in the process, it is necessary to use the system concept and system method to solve the problems of the tool in the process, and take corresponding measures. Zhang Taihe, chief engineer of Henan Fenike Superhard Materials Co., Ltd. concluded that: pay attention to every link of tool selection, pay attention to every link of tool application, pay attention to every link of cutting process, and find out the suitable method for tool application. You will get results that are half-worked.
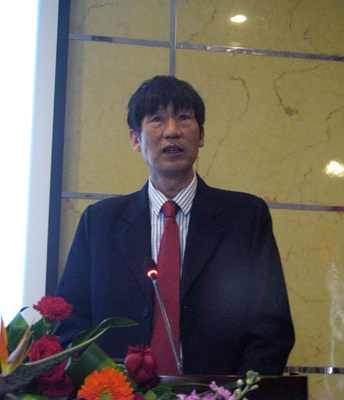
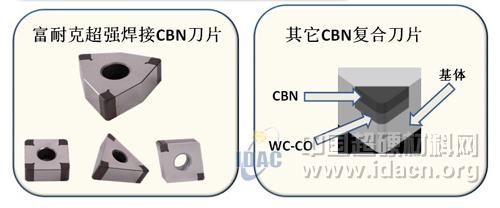
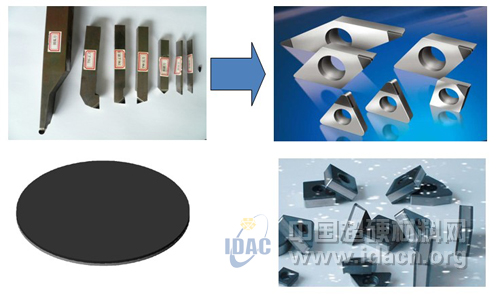
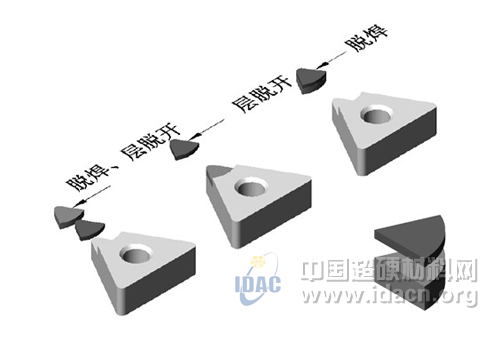
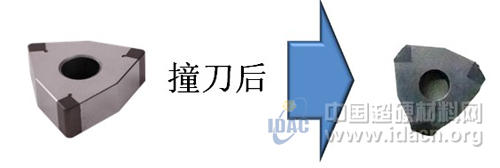
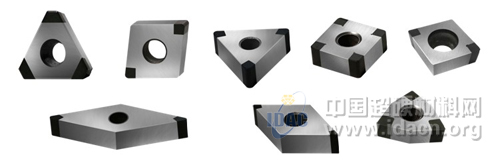
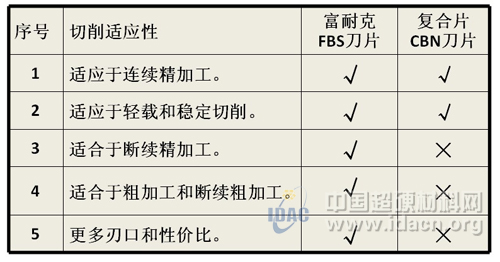
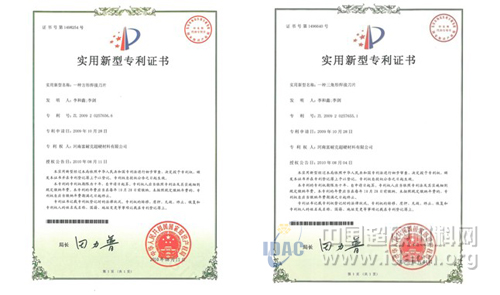
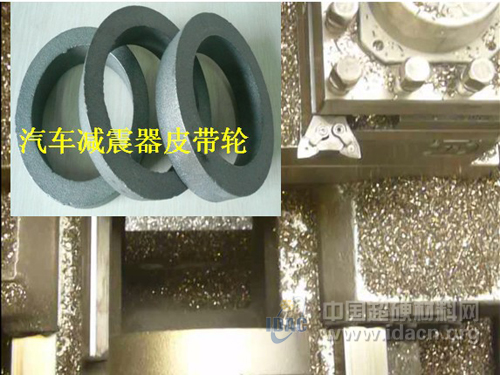
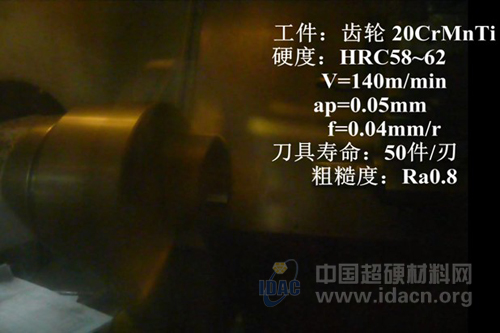
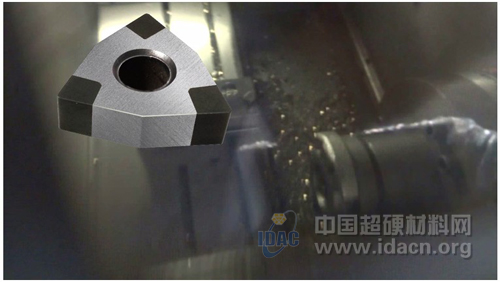
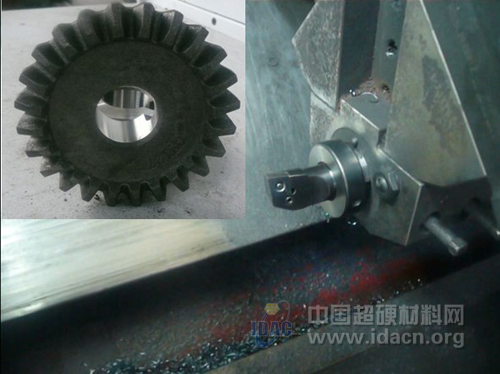
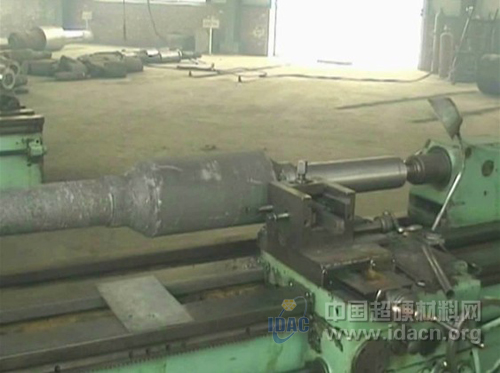
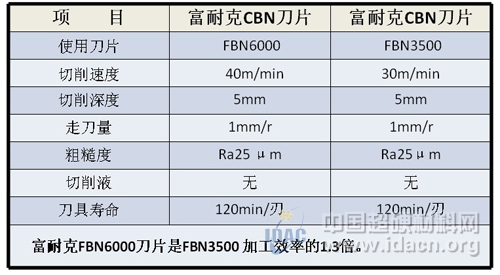
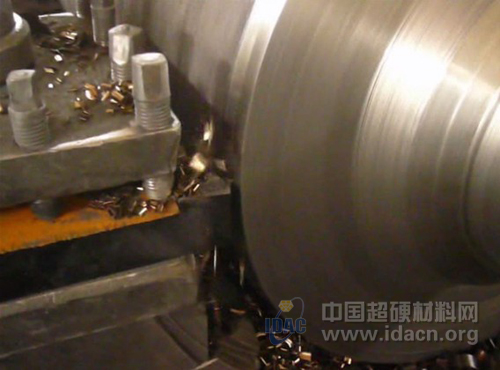


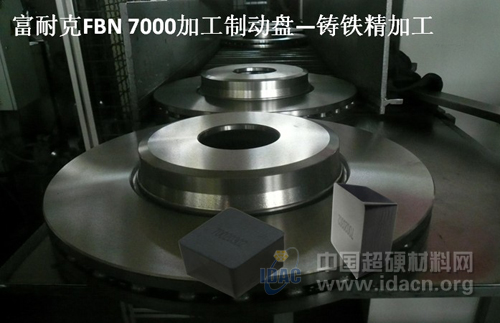
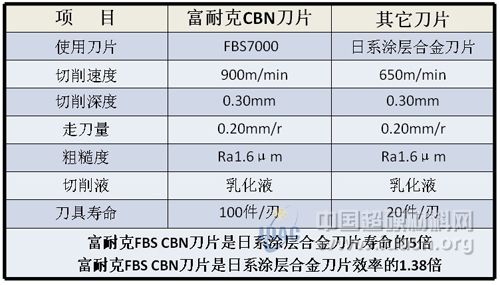

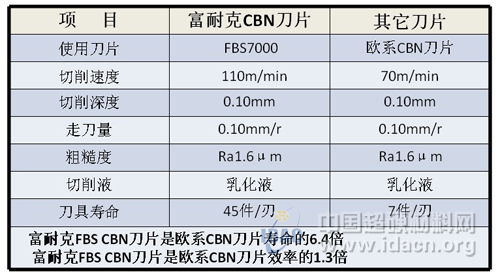
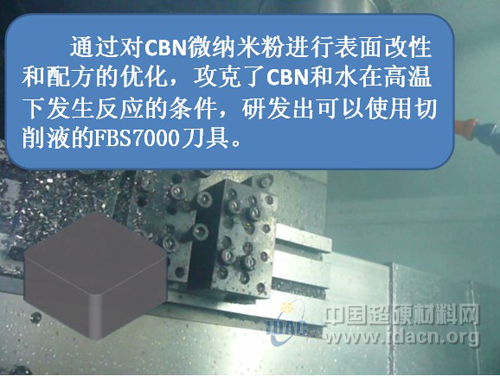
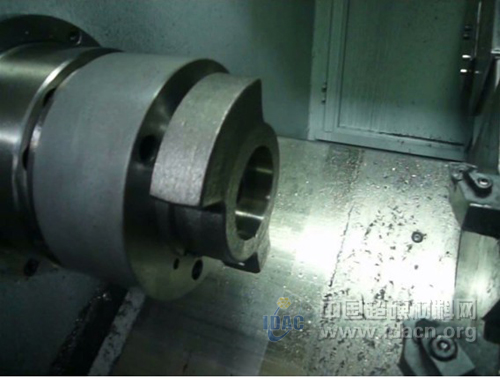
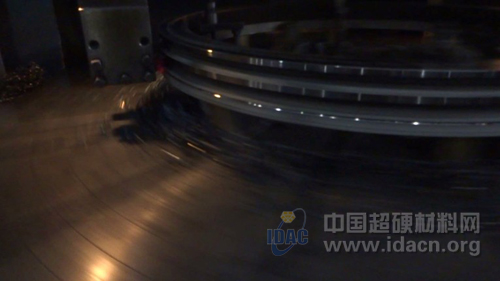
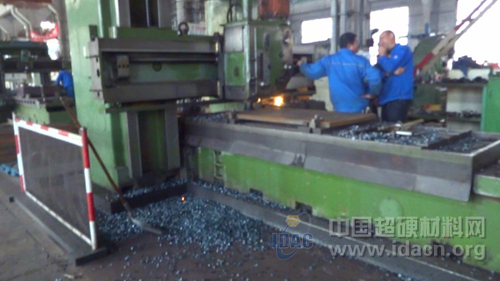
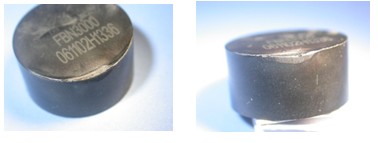
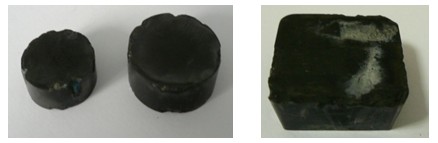
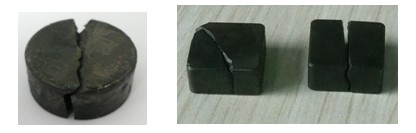
Led Light Pad,Dgital Tracing Pad,Led Light Board For Drawing,A5 Tracing Pad For Kids
Guangdong Jishengke Industrial Co., Ltd. , https://www.suronart.com