HAILAN Sea Blue J Series Plunger Metering Pump Section 1 Description HAILAN Sea Blue J Series Plunger Metering Pump (hereinafter referred to as the pump) is a reciprocating displacement control pump, which can be used to transport a specific volume by adding a positive pressure difference to the pump inlet and outlet Of the liquid, the delivery error can be controlled within ± 1% of the set value.J Series piston pump is particularly suitable for precision liquid transfer. Pump head packing imported GFO ○ R packing to solve the packing seal life is short The pump consists of three main parts: (1) drive part: including motor, worm, worm gear, eccentric crankshaft, connecting rod, etc .; (2) hydraulic part: including pump head, plunger, ) Adjustment section: including the adjustment table, adjust the gearbox, adjust the screw, etc. The displacement of the pump is a function of the number of strokes, piston stroke length and piston diameter.Moreover, a metering pump displacement by pump stroke length Mechanical adjustment (precision adjustment screw) or by frequency motor adjustment stroke number to change (optional) This manual contains the series of metering pumps, mechanical drive, regulation and the hydraulic end part of the content of the operation of the principle drive Pump plunger, inhalation stroke will liquid Body sucked into the pump head cavity, and in the subsequent discharge stroke of the liquid discharge, only when the discharge pressure is greater than the suction pressure, accurate flow control can be obtained.HAILAN sea blue J series metering pumps using the "N" shaft drive - It has the advantages of large bearing capacity, reliable operation, convenient adjustment, etc. Its essence is that the worm gear mechanism drives the "N" shaft, the "N" shaft drives the crank rod to reciprocate, and then the connecting rod drives the crosshead to slide The linear motion of the shoe allows the stroke length of the pump to be varied from zero to the maximum by adjusting the "N" shaft so that the connecting rod is in a different position on the "N" shaft. Each suction stroke, plunger retraction, Through suction check valve into the pump head cavity .Each discharge stroke, the plunger is pushed out of the process medium through the discharge check ball valve out of the pump head cavity .Each suction stroke, exhaust check valve ball is closed, each discharge stroke, Suction check valve is closed This mode of operation prevents media backflow and ensures that media enters the suction valve and exits the discharge valve through the pump head cavity Safety Warning When installing, operating, and maintaining a HAILAN sea blue pump, safety should first be considered When operating the equipment, use appropriate tools and protective clothing Goggles, installation should pay attention to the installation of equipment to ensure safe operation. Follow the instructions in this manual, for different transmission media should be used with additional safety measures, there should be more careful when dangerous media (such as corrosives, toxic substances, Acid, alkali, combustibles, etc.) Section 2 Installation Unpacking The Company's pump is handed over to the user by the carrier, and all damages that occur during transit should be immediately notified to the carrier and claimed.Users before the official receipt, Carefully inspect the shipping package to verify that no damage has occurred during shipment, open the package and verify that all items, including attachments, are in good condition, in the correct quantity and checked with the "packing list." Installation Install the pump horizontally (with shims ), Firmly supported on a solid, vibration-free basis, and then supported by a base above ground level, so that it is flooded during flushing and easy to handle. The pump mounting holes are compatible with the anchor bolt holes , It is very important (some HAILAN sea blue pump transport motor is not installed, the pump installed in place, the installation of the motor) General rules for pipe connections Use pipe resistant to transport medium corrosion, the choice of materials should be considered Thoughtful to prevent galvanic corrosion at the pump fluid connection; use thick enough tubing to withstand maximum system pressure; and pipe size to accommodate peak instantaneous flow. Pump delivery follows an approximately sinusoidal peak due to reciprocation of the pump plunger, peak The instantaneous flow is 3.14 times the average, so the line should be designed to pass a flow of 3.14 times the displacement of the pump, which means that a pump rated 100 L / h needs to pass 100 L / h × 3.14 = 314 L / h In order to reduce the viscous flow loss, the viscous fluid pipeline should be 4 times larger than the pump port. The burr, sharp edge and dross in the pipeline should be removed, and the pipeline should be purged during the final connection between the pump and the pipeline. When using fluid, use expansion joints and support the pipe so that the weight of the pipe is not applied to the pump Do not twist the pipe when making connections; the pipe should be tilted to prevent steam pockets as the steam pockets at the fluid end Affect the delivery accuracy of the pump, and when transporting liquids (such as mud) with suspended solids, install a screwed cross-over at all 90 ° turns to allow for pipe cleaning without dismantling the pipe. Suction pipe inlet placed in the lowest level of the water tank to pump Inlet Immersion. Installing a support tower or water supply near the pump suction line helps to ensure that the suction end is immersed (consult our company for assistance). Negative suction pressure conditions (suction lift) should be avoided because this condition If this condition is unavoidable, please contact our technical department for advice. If the fluid being delivered is close to the boiling point, provide enough suction pressure to prevent the liquid from entering the liquid end instantly vaporizing "For steam, metal or plastic tubing should be used on the suction lines, if possible, because they have a smooth inner wall to create long, large diameter bends that reduce frictional resistance. Filters should be used on suction lines to prevent foreign Particulate ingress into the tubing (this, along with other measures to prevent dust ingress and fouling on the check valve, will increase maintenance-free use time.) Filters should always be inspected to prevent clogging, as clogging can lead to cavitation. The suction tube should be as short and straight as possible. When the suction tube is long, especially when the stroke speed of the pump is greater than 70 spm, the line size should be larger than the suction tube diameter of the pump to prevent insufficient pump suction. Too long Inlet pipe inevitably, a float tank or auxiliary tank (tank) should be installed on the suction side of the pump, the float tank can be calibrated, and the flow of the pump can be measured by measuring the time it takes to pump a certain amount of water from the tank. In many cases, installing a pressure accumulator or pulsation damper on the pump inlet manifold will help pump self-priming, even if the suction line is long. For detailed knowledge, contact our technical department. The suction line should be absolutely sealed, In order to ensure accurate delivery of the pump. After installation, check the tightness of the suction pipe with air and soapy water. Exhaust pipe Install a pipe of sufficient internal diameter to prevent excessive pressure loss during discharge of the pump. Maximum rated pressure on the liquid outlet pipe The pump controls the output flow only when the discharge line pressure is greater than the suction line pressure Ensure that there is a positive pressure differential of at least 5 psi between the discharge side and the suction side. There are many ways to manually increase the pressure at the discharge side, such as by using a backpressure valve.) Use a liquid-end assembly for each boiler drum when delivering water treatment chemicals directly to the boiler drum. Discharging to the manifold will reduce metering accuracy Although at The pressure difference between the discharge pipes is extremely small, but the outlet with the lowest pressure will be larger than the other discharges.The pulsation damper (pressure accumulator, surge chamber, etc.) should connect the accumulator, surge chamber, The pulsation damper, together with the backpressure valve, is used to drain the line to absorb the peak flow between the pump and the backpressure valve. Without a pulsation damper, the backpressure valve mechanism will be pulsated with each stroke of the pump The rapid switching, pulsation damper allows the back pressure valve in the half-open position of vibration, thus reducing the valve wear and tear. Exhaust pipe set pulsation damper, as well as to improve the pump pressure and flow characteristics of the advantages of setting the appropriate size The pulsation damper will improve the performance of the pump and reduce the cost of the system significantly with smaller piping. For more detailed knowledge on pulsation dampening, contact our company. Back Pressure Valve Back Pressure Valve, Discharge pipe near the pump head to provide sufficient discharge head to ensure that the metering pump metering role usually in the vicinity of the pump, but for a very long and small diameter discharge pipe pump must be set at the dosing point (To reduce siphonage). Safety valve overheated The motor can still drive the metering pump before the protective device is disconnected from the motor circuit, which can generate huge discharge pressure. To prevent the pump, pipeline or other equipment from being damaged due to the blockage of the discharge pipeline, the discharge pipe of the pump should be set Safety valve. The design of the valve: its size can safely control the system flow and pressure, and resistant to the transmission medium corrosion. Safety valve is set in the discharge line between the pump and the nearest shut-off valve (which will be in the valve when the valve is closed or blocked accidentally , To avoid damage to the pump.) Safety valve outlet connected to the tank or drain, but either way, should ensure that operators can always see the end of the pipeline and relief valve discharge situation. A check valve shall be provided where the discharge line enters the boiler or other high pressure vessel. This valve will prevent backflow through the discharge line and isolate the pump discharge from the system pressure. Close to the pump, set the shutoff valve. The shutoff valve on the discharge line should be located downstream of the safety valve inlet port. Equipment Operation Connect the Pump Drive Before wiring, check the nameplate on the pump drive motor and confirm the power supply If not, an arrow indicates the correct direction of rotation of the motor shaft at the pump-end flange This additional protection will protect the thrust in the opposite direction resulting in the release of the thrust bearing This series of metering pump packings are manufactured using a U.S. imported GFO ○ R Packing, to ensure that under 100kgf / cm2 pressure does not leak, and have a longer life .Third operationOperation for the first time check the tightness of all the mounting bolts to confirm that the receiver is installed correctly, and the discharge line has been opened in the pump Gear box filled with gear oil, the oil surface is added to the center of the oil window so far. The gear oil is poured into the housing bearing box worm pay, cover the fuel tank cap.According to the arrow on the pump housing, connected to the pump motor So that it rotates in the direction of the arrow Note: When the ambient temperature is low, the viscosity of the gear oil will increase, therefore, in different temperature conditions, in order to prevent the pump motor overload, you should use different types of gear oil. The table below lists the suitable gear oils for different temperatures Gear Oil Estimated Minimum Environment Temperature Gear Oil Grade Winter Use 220 Summer Use 320 Initial Conditioning Plunger Packing Before running the pump, run the packing as follows: Tightly sealed Set until a certain resistance can be felt. After 15 minutes, release and tighten until a certain resistance is felt.
CNC Milling Machine
SF factory is focus on quality and company's image. We win market with good quality and service. The company has already passed International Quality Management System ISO9001:2008 certification for many years and also got the CE certificate, smoothly got the title of High and New Tech Enterprises.
And has more than ten own intellectual property rights and patent technology. We have own import and export right. Our products exported to Russia, South Asia, South east Asia, Middle East, South America, Africa, Australia, Eastern Europe etc.
CNC Professional machine for Steel coil.
Products Mainly including:
Steel coil recoiler.
Steel coil uncoiler;
Steel coil uncoiler and shearing machine
Steel coil uncoiler and slitting machine;
Plate Punching Machine;
Plate Drilling Mchine;
Beveling Machine;
Shandong SF CNC Machinery Co., Ltd. is a grand manufacturer of
Transmission tower machines in china. With 23 years` experience in this line, we are committed to
producing only the finest products to our customers.
In 2019, we appointed Jinan JUFU International
Co.,ltd to specially export our machines to abroad markets. And now we have a
special engineer team for oversea market, and we are able to offer customer
timely service.
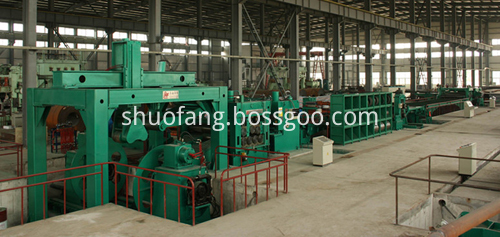
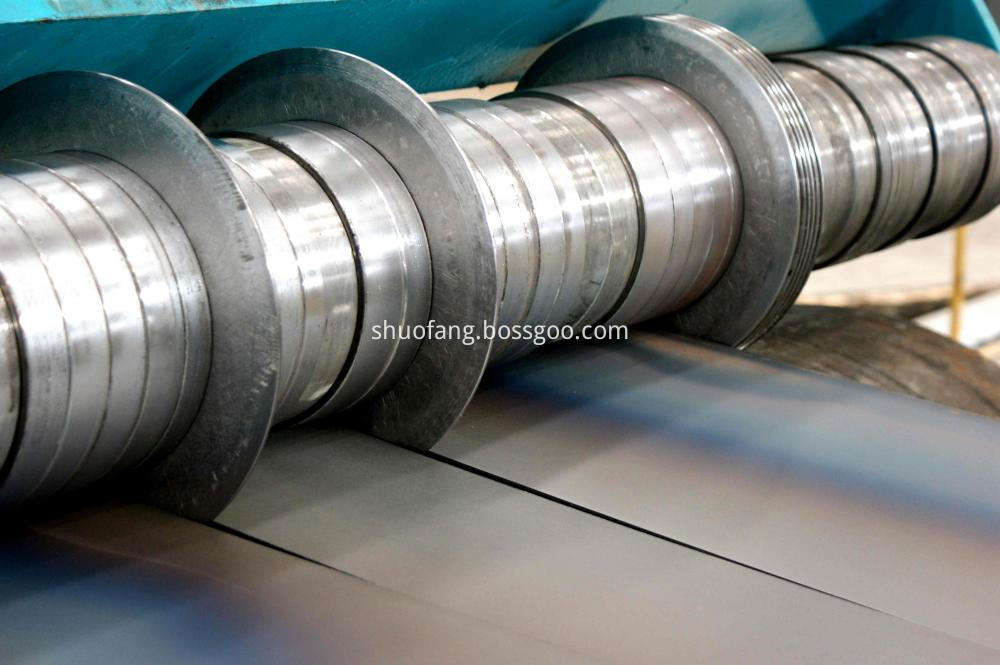
Steel Punch Machine,Steel Plate Machine,Steel Coil Slitter Machine,Steel Plate Drilling Machine
Shandong EN FIN CNC Machinery Co., Ltd , https://www.sdfincnc.com