Factors Affecting Peel Strength of Aluminum Honeycomb Panels
ã€China Aluminum Industry Network】 1. Impact of Adhesives on Peel Strength of Aluminum Honeycomb Panels (1) Aluminum Honeycomb Panels made of Polyurethane and Epoxy Resin Room-Temperature Curing Adhesives have a low bonding strength and a honeycomb core length of 4mm. The aluminum honeycomb panel with a panel thickness of 1 mm and a total thickness of 10 mm measures a 180° peel strength of about 4 N/mm. This aluminum honeycomb panel has poor adhesiveness and weather resistance, and its adhesive performance is greatly reduced after one year of use. Aluminum honeycomb panels produced using this process are not suitable for outdoor use, but can be used indoors as decorative partitions.
(2) The adhesive strength of the aluminum honeycomb panel produced by the epoxy film process is low. For the honeycomb core length of 4mm, the panel thickness is 1mm, and the aluminum honeycomb panel with a total thickness of 10mm has a measured peel strength of 4O[deg.]. About mm/mm, however, the weatherability of the adhesive performance is good, and the peel strength decreases a little after one year of use. The disadvantage is that the adhesive layer of the aluminum honeycomb panel is relatively brittle, and the aluminum honeycomb panel will delaminate after long-term vibration.
(3) The adhesive strength of the aluminum honeycomb panels produced by continuous compounding technology of thermoplastic films is 3-5 times that of the aluminum honeycomb panels produced by the first two processes, and the length of the sides of the hexagonal honeycomb cores is 4 mm, and the panel thickness is For a 1 mm aluminum honeycomb panel with a total thickness of 10 mm, the 180° peel strength measured is about 18 N/mm. The adhesiveness and weather resistance are good, and the peeling strength decreases little after one year of use. Due to continuous production, high efficiency can meet short-term and large-scale supply requirements. The disadvantage of this process is that the flat continuous thermal compounding machine used is expensive and the investment is huge. Thermoplastic film is a kind of special hot-melt adhesive film. The film itself must have high cohesive strength and tensile strength, which can ensure the firm bonding of aluminum honeycomb panels. If a general hot melt adhesive film is used, its adhesive strength is very low and the 180° peel strength value is only 3 N/mm.
2. Effect of Production Process on Peeling Strength of Aluminum Honeycomb Panels Using heat presses to produce aluminum honeycomb panels, due to the high pressure of hot presses, it is difficult to control. In order to prevent collapse of aluminum honeycomb cores, pads are often placed. If the pad is high, the applied pressure will be affected, resulting in low adhesive strength. If a planar thermal laminator is used, since the pressure is provided by the elastic force, the applied pressure can be controlled by adjusting the height. Therefore, the aluminum honeycomb panel produced by this process has higher bonding strength and is stable.
3. Effect of surface conditions of aluminum on the peel strength of aluminum honeycomb panels The oily dirt, dirt, and naturally formed loose oxide layers on aluminum surfaces can seriously affect the bonding effect of aluminum honeycomb panels. Therefore, they must be cleaned and pretreated. The surface of the aluminum can be phosphatized or chromated to form a layer of chemical conversion film on the surface of the aluminum. The treated aluminum has a good bonding effect.
Metal steel frame screens main feature as follows:
1.These products screen panels are constructed with two or three 304 or 316 stainless steel wire cloth layers with s steel backing plate and steel frame combined together. Because of different mesh size and hole size, get an better filtering effect.
2.The bottom high strength steel frame, supporting bar with the moderate tension screen cloth, combined together, infinitely enhance the screen intensity and endurance, get an better filtering effective. Mesh sizes ranging from 20to 325. The whole cloth is divided into independent small surfaces, prevent the part excessive expansion damaged, with a special rubber plug together to repair damage, can save the time to replace the screen, Increase the efficiency and reduce the cost.
Metal Steel Screen Common Model |
||||
Model | Brand&Model for shaker | Mesh Range | Dimension(Length xWidth | Weight |
SJ-1 |
Brandt BL-50 |
40-325 | 1253X635mm | 13.5KGS |
SJ-2 |
Swaco Mongoose |
40-325 |
1165x585mm | 14KGS |
SJ-3 |
Kemtron 48 Series |
40-325 |
1220x720mm | 17.5KGS |
SJ-4 |
Kemtron 48 Series |
40-325 |
913x650mm | 12.6KGS |
KING COBRAâ„¢ VENOMâ„¢ Shaker is manufactured by National Oilwell Varco (NOV), a oilfield service company based in the USA with branch company in most oil reach countries.
NOV Brandt King Cobra Screen is pre-tensioned screen and wedged installation.
NOV Brandt King Cobra Screen | |
Mesh Size | API 20 – API 400 |
Dimension | 1253mm x 630mm (49 1/5″ x 24 4/5″) |
Frame Material | Steel Frame |
Wire Mesh Material | S.S304 or S.S316 as per request |
Screen Layer | 2 or 3 Layers |
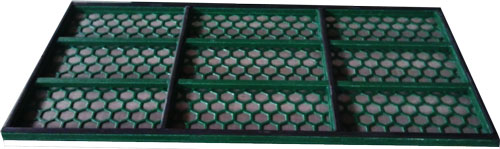
Metal Steel Frame Shale Shaker Screen
Shale Shaker Screen,Oil Shale Shaker Screen,Conventional Metal Frame Shaker Screen,Industrial Shale Shaker Screen
Anping Shengjia Hardware Mesh Co.,LTD , http://www.oilshaleshakerscreen.com