How do you know about the university in the production of plastic bottles?
Klear Can plastic cans
In recent years, plastic machinery manufacturers have been accelerating technological innovation in the field of packaging applications, and we have indeed seen a big leap in plastic packaging products, from the common beverage bottle caps to the brand-name cosmetic cans on the tall, all contain plastic processing technology. Asked by the university. Today we will come through these several cases to take stock of the advanced technology in the production of plastic bottles and cans.
Integrated injection blow molding process
Injection blow molding enables economical production of ready-to-use small containers in a single operation, however, the number of cavities that can be achieved has heretofore been limited. Together with its system development partners Foboha and alpla Werke alwin Lehner, ENGEL has successfully developed an integrated process that, combined with the use of multi-cavity molds, significantly reduces cycle times. Based on cube technology, the number of cavities can be increased without affecting cycle time and accuracy, which greatly reduces the unit cost at high throughput.
ENGEL e-motion 740/220 T WP all-electric injection molding machine with 8-cavity cube mould
At the K2016 show, ENGEL demonstrated the potential of the new injection blow molding process in the packaging industry. ENGEL produces polypropylene containers through the e-motion 740/220 T WP all-electric injection molding machine and is equipped with an 8-cavity cube mold. These polypropylene containers were developed by Alpla for a customer in Asia and until now, the customer's products are still packaged in glass containers. When polypropylene replaces the original glass material, it can reduce production cost and package weight, while improving the safety of consumers.
In order to shorten the cycle time, the previously pre-produced preforms are placed on the opposite side of the mold parallel to the injection molding station to complete the blow molding. At the same time, the ENGEL EASX six-axis robot integrated in the production unit takes the finished containers from the fourth station and places them open on the conveyor belt. The entire process is carried out simultaneously with the injection molding without increasing the cycle time. In the second station, an insulated cover is used to prevent the preform from cooling, and the injection volume per container is 8 grams.
In this integrated process, the partner of the blow molding system is France's Bauer Compressors. As part of the integrated process, the gas pressure can be controlled by the CC300 control system of the ENGEL injection molding machine.
In the process of technology development, pay special attention to the consistency and accuracy of the process. The container body and threads can be kept to a minimum tolerance, and the entire process can produce a reproducible high quality container only if the preform has exhibited a very consistent wall thickness.
The all-electric drive technology of ENGEL e-motion injection molding machine has made a huge contribution to zero defect production. In particular, the iQ weight control and iQ clamp control intelligent assistant systems are very important in the application. Through continuous analysis of key process parameters, even with small changes in the environment and raw materials, the injection molding machine can automatically monitor and compensate in the same shot. In addition, temperature control also has an impact on quality. Six ENGEL e-flomo manifold units with four temperature regulation circuits, each responsible for continuous detection and flow mastering.
Arburg produces a two-color clamshell cap for Pril detergent bottles from Henkel via an allrounder Cube 2900
This integrated process technology opens up a wide range of possibilities for advanced injection blow molding technology. In addition to polypropylene containers, the process is also suitable for items such as baby bottles or cosmetic cans. If applied to the pharmaceutical industry, the entire system can meet cGMP standards.
Innovative clamshell cap production
Rotary die technology has become particularly interesting when more machines are needed under the conditions of conventional technology in order to achieve the required sales volume. Because, with four solid faces for manufacturing and two continuously placed parting faces, the rotary die provides a decisive advantage: individual process steps, such as mold filling, cooling or pick-up, are done simultaneously. Other processes, such as embedding, installing, or detecting, can be integrated without changing the cycle time. In the case of the same mold mounting area, double the number of cavities. In this way, the rotary mold doubles the output and reduces the unit cost.
At the 2016 K show, Arburg used an allrounder Cube 2900 with a 32+32 rotating die from partner Foboha to produce a two-color clamshell cap for Henkel's Pril detergent bottles. The total cycle time is 8.5 seconds and the weight of the two-component injection molded PP material is 3.2 grams. The allrounder Cube machine on display is designed for high-speed rotary tooling applications. The rotary die has four available faces, and the processing of preforms and finished products as well as cooling and demolding can be performed simultaneously. Mr. produces a 0.8-gram droplet-shaped upper half as the first component, and after cooling the second surface, injects 2.4 grams of the second component at the third station, and finally on the fourth mold surface. Demold the flip cover and place the lid on a separate workstation. The visual quality inspection of the machined parts was done by five high-resolution cameras from Intravis.
Arburg optimized the entire clamping unit, including the servo-electric crank lever, according to the technical requirements of the cube mold. Thanks to the short dry cycle time, the cycle time can be reduced by another by 1 second with a new cube mould and the output is increased by 10%. The spacing between the Corinthians has also increased, with a spacing of 820 mm on the allrounder Cube 2900. Another advantage is the significantly increased mold mounting size on the clamping unit, with a maximum size of 1900 mm on smaller machines and 2400 mm on larger machines, which means installations can weigh up to 16 Tons of mold.
The standard new cube moulding machine has four servo electric shafts: one for the clamping unit, two for the electric feed and the last for the mould. The injection unit can be hydraulically or electrically driven, and the ejection core and more mold functions are hydraulically driven. This design concept reduces energy consumption by up to 45% compared to conventional hydraulic machines.
In close cooperation with Foboha, Arburg has implemented a complete production system for single or multi-component production based on an accurately matched allrounder Cube machine.
In addition, Husky presented two fully integrated cap systems for the first time at K 2016. Husky has made significant improvements to the newly introduced HyCaP 4 system for beverage closures, with higher integration of machines, molds and auxiliary equipment to increase productivity, improve energy efficiency and enhance ease of use. The system produced 1.25 grams of 29/25 mineral water bottle caps on-site in a 2.4 second injection cycle.
At the same time, Husky also exhibited for the first time its latest professional bottle cap manufacturing system solution HyperSync. HyperSync produced a 6.1 gram shampoo flip in a very short injection cycle of 8.5 seconds. The fully integrated eIMC in-mold closure technology provides more precise control during the injection stroke, allowing safe stacking of mold functions, improving product quality while reducing injection time by more than 20%.
Plastic packaging can replace traditional metal packaging cans
For food manufacturers, traditional metal packaging cans have been the only packaging material that can isolate oxygen and meet the needs of food sterilization, anti-corrosion, etc. Nowadays, plastic packaging manufacturers have been able to provide the same as metal packaging cans. Performance plastic packaging to replace traditional metal cans.
The multi-layer recyclable Klear Can series of plastic cans from Milacron have successfully passed the most stringent food safety testing in the United States. This plastic can is a perfect replacement for metal cans in fruits, vegetables, soups, meat products and Many other applications on the product. Recently, Milacron Group confirmed the sale of the first Klear Can production system, and Klear Can plastic packaging cans is expected to log into retail stores in the first quarter of 2017. The advantages of Klear Can cans are obvious. Consumers can clearly see the quality of the food at the time of purchase. The entire package does not contain BPa, and the filling, sealing and sterilization techniques can be used in the same way as metal cans, thus minimizing downstream Investment costs of production machinery. In addition, manufacturers can also produce and shape Klear Can series plastic packaging cans in the filling and filling process. Compared with metal packaging cans, Klear Can series plastic packaging can effectively reduce production costs and have a competitive advantage. In addition, companies can also win the favor of more consumers by showing consumers the safe and high-quality features of this Klear Can series of plastic cans.
At the 2016 K show, Milacron displayed the in-mold labeling of the Klear Can series of plastic packaging cans on the stand, and the entire production was carried out on the Ferromatik series. The Ferromatik range of machines is designed to handle the fast cycle times and high injection speeds of the packaging industry. There are currently nine sizes with clamping forces ranging from 120 to 650 tons, pre-configured with multi-component, sandwich and cube mold production techniques. And it can be configured as all-electric, hydraulic and liquid-electric composite according to different needs.
The fastest in-mold labeling application
Over the past 20 years, high-speed El-Exis has evolved into the most important machine for plastic packaging applications. Sumitomo Demag has been updated over several generations and continues to increase its range of clamping forces. El-Exis SP's current clamping force covers a range from 1,500 to 7,500 KN. More than 2,000 El-Exis SP injection molding machines are currently installed in thin-wall plastic packaging, screw caps and various sealing covers. El-Exis has recently been updated with energy optimization and is equipped with an OPC/Ua communication interface that complies with the Industry 4.0 standard.
Sumitomo Demag showed the fastest in-mold labeling application at K 2016, completing 4 decorative cups in less than 2 seconds. The El-Exis SP 200 high-speed injection molding machine produces decorative cups in four cavity molds. The high-speed pick-up robot enters the parting surface from the side, puts the label into the fixed mold, and then removes the four already formed cups on the moving mold. These cups are then stacked. This machine demonstrates the fastest speeds and highest system productivity that can be achieved with in-mold decorative plastic containers. With less than 2S cycle time, the El-Exis SP 200 is probably the fastest machine for producing decorative containers at K2016.
New PET bottle bottom technology
Sidel introduces the new StarLite Nitro non-petal bottom, which has a unique shape that significantly enhances bottle bottom stability and resistance. This also means that the new bottle bottom can increase the hardness of the PET bottle, have stronger resistance to the internal pressure caused by nitrogen injection, and have higher adaptability to the environment; at the same time, the package weight and production energy consumption are reduced. In addition, it makes the packaging design distinctive and more aesthetic, and ensures the safety of the interior products.
The Sidel StarLite Nitro bottle bottom improves the quality of the bottle while maintaining the strength of the package and improves the stability of the bottle throughout the supply chain. The design of the bottom of the bottle is large, the stability is good, and the structural design elements of other bottles make the PET bottle more resistant to the internal pressure brought by the nitrogen injection, and also improve the bottle during the delivery. Stability (depending on the thickness of the bottom of the bottle). This is particularly advantageous for products that are produced at high latitudes and then sold at low latitudes, but also for applications at very high temperatures. The new bottom is developed by Sidel packaging experts and tested using a variety of computer simulation techniques, as well as physical testing under real-world conditions to ensure optimal performance throughout the supply chain.
- Previous: How to solve the problem of flowering in plastic products, Xiaobian teaches you all the seven strokes
- Next: Analyzing the similarities and differences between the two processes of "blowing method" and "casting method"
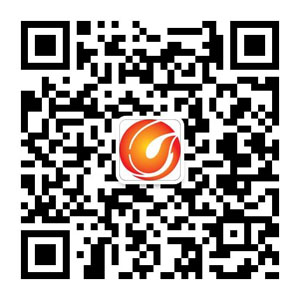
Pay attention to the recycler network WeChat public platform, you can enjoy unprecedented VIP-level enjoyment, daily push quotes, asset disposal, auction bidding and other massive information, and all this is free! What are you waiting for, pay close attention to me!
Ningbo Kyson Cool Electronic Technology Co., Ltd. , https://www.kysonrefrigeration.com